SCOPRI IL NOSTRO CANALE YOUTUBE
Come si trasporta e come funziona un Rigassificatore di gas naturale liquido?
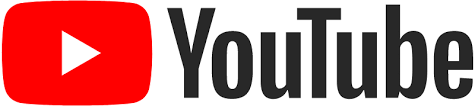
Come si trasporta e come funziona un Rigassificatore di gas naturale liquido?
In un nostro precedente video abbiamo parlato del gas naturale e le sue caratteristiche, vedendo nel dettaglio tutti gli step necessari per la sua estrazione e le tipologie di impianti.
Come abbiamo già detto, il gas una volta estratto viene raffinato e trasportato, attraverso gasdotti o metanodotti, ad impianti elettrici e abitazioni domestiche.
Ma come avviene il trasporto del gas estratto dal giacimento al suo fruitore finale? Nella migliore delle ipotesi, viene trasportato via terra con l’ausilio di metanodotti, per territori che hanno la fortuna di essere collegati a paesi fornitori, come la maggior parte dei paesi europei con la Russia. Per paesi invece che non hanno queste possibilità, devono acquistare il prodotto da nazioni che effettuano il trasporto del gas naturale via mare.
Il trasporto via mare del gas naturale è molto delicato, parliamo di un prodotto composto per il 98% da metano, altamente infiammabile, e trasportarlo in grossi serbatoi installati su di una nave può essere particolarmente rischioso.
Ecco perché bisogna portare il gas naturale dal suo stato aeriforme allo stato liquido. Il gas naturale liquido, detto anche GNL (LNG in inglese), non è infiammabile come nello stato aeriforme, inoltre il volume del gas si riduce di 600 volte, agevolando e aumentando la capacità di trasporto delle navi metaniere con un singolo viaggio. Le navi metaniere sono speciali imbarcazioni costruite appositamente per il trasporto di metano e gas infiammabili.
Ora vediamo nel dettaglio la filiera di distribuzione e trattamento del gas naturale.
Dopo l’estrazione del prodotto, con l’ausilio di metanodotti, il gas viene trasportato in degli speciali impianti che procederanno alla sua liquefazione; gli impianti possono trovarsi vicino alle coste, normalmente in zone portuali, oppure in impianti off-shore, con strutture galleggianti ancorate al fondo marino.
Per portare il gas allo stato liquido, si inizia con un trattamento di rimozione dell’anidride carbonica e dell’acido solfidrico, successivamente si effettua un preraffreddamento e si procede con l’estrazione di eventuali componenti pesanti. Arrivati a questo punto si abbassa drasticamente la temperatura del gas a -163°C, al dì sotto della temperatura di ebollizione del metano, principale componente del gas naturale.
Con tubi criogenici, situati su pontili di caricamento, viene iniettato il gas naturale liquefatto all’interno di serbatoi posti sulle navi metaniere. Queste particolari navi possono trasportare dai 150 ai 200 mila metri cubi di metano, e ne esistono di due tipologie:
- Il primo esempio è quello di nave con serbatoi integrati sviluppati dalla Gaztransport & Technigaz. Per questa tipologia esistono 2 versioni: quella della Technigaz con serbatoi costituiti da una barriera primaria elastica, formata da una membrana con nervature realizzata con lastre di acciaio; la disposizione delle lastre forma due ordini di nervature ortogonali tra di loro ed hanno la funzione di ridurre le sollecitazioni termiche. La barriera secondaria è realizzata con un materiale composito, il “triplex”, costituito da un foglio di alluminio in un wafer di tessuto di fibre di vetro. Il serbatoio è fissato allo scafo interno con una schiuma di poliuretano rinforzata con fibre di vetro. La tipologia messa a punto dalla Gaztransport invece prevede due barriere costituite da fasciame piano saldato, fatto di una particolare lega metallica di acciaio e nickel, chiamato invar. Tra le due barriere sono presenti dei pannelli isolanti e delle camere d’aria, nella quali vieni iniettato dell’azoto liquido per mantenere la temperatura criogenica del gas naturale. In questo caso il serbatoio è tenuto allo scafo interno con delle scatole di isolamento termico in legno di balsa riempite di perlite.
- Altro esempio di nave metaniera e con serbatoi autoportanti: la società Moss Rosenberg affrontò il problema della resistenza alle sollecitazioni indotte dal peso del gas naturale nei serbatoi, per risolvere progettò metaniere con 4 o 6 serbatoi sferici. Le sfere sono isolate con uno strato di materiale isolante, tra di esse viene fatta passare un’intercapedine riempita con azoto per aumentare la capacità isolante e mantenere bassa la temperatura del serbatoio. Ogni sfera è sostenuta da una camicia cilindrica che poggia sullo scafo della nave; quest’ultimo viene protetto da eventuali fughe di gas con una barriera secondaria posta alla base delle sfere.
La metaniera trasporta il suo carico di GNL sino all’impianto di rigassificazione; dopo essere state ancorate e aver effettuato la connessione ai bracci di scarico degli impianti del porto, iniziano a trasferire il GNL nei serbatoi di stoccaggio. Gli impianti di rigassificazione possono trovarsi in zone portuali, quindi parliamo di un impianto onshore sulla terraferma, oppure di una piattaforma, appoggiata sul fondo marino, che prende il nome di offshore gravity based, o ancora di una floating storage and regasification unit, FSRU, una nave metaniera, convertita per la rigassificazione, ancorata al fondale marino, ma questa tipologia la vedremo più avanti.
Come abbiamo già detto, il gas una volta estratto viene raffinato e trasportato, attraverso gasdotti o metanodotti, ad impianti elettrici e abitazioni domestiche.
Ma come avviene il trasporto del gas estratto dal giacimento al suo fruitore finale? Nella migliore delle ipotesi, viene trasportato via terra con l’ausilio di metanodotti, per territori che hanno la fortuna di essere collegati a paesi fornitori, come la maggior parte dei paesi europei con la Russia. Per paesi invece che non hanno queste possibilità, devono acquistare il prodotto da nazioni che effettuano il trasporto del gas naturale via mare.
Il trasporto via mare del gas naturale è molto delicato, parliamo di un prodotto composto per il 98% da metano, altamente infiammabile, e trasportarlo in grossi serbatoi installati su di una nave può essere particolarmente rischioso.
Ecco perché bisogna portare il gas naturale dal suo stato aeriforme allo stato liquido. Il gas naturale liquido, detto anche GNL (LNG in inglese), non è infiammabile come nello stato aeriforme, inoltre il volume del gas si riduce di 600 volte, agevolando e aumentando la capacità di trasporto delle navi metaniere con un singolo viaggio. Le navi metaniere sono speciali imbarcazioni costruite appositamente per il trasporto di metano e gas infiammabili.
Ora vediamo nel dettaglio la filiera di distribuzione e trattamento del gas naturale.
Dopo l’estrazione del prodotto, con l’ausilio di metanodotti, il gas viene trasportato in degli speciali impianti che procederanno alla sua liquefazione; gli impianti possono trovarsi vicino alle coste, normalmente in zone portuali, oppure in impianti off-shore, con strutture galleggianti ancorate al fondo marino.
Per portare il gas allo stato liquido, si inizia con un trattamento di rimozione dell’anidride carbonica e dell’acido solfidrico, successivamente si effettua un preraffreddamento e si procede con l’estrazione di eventuali componenti pesanti. Arrivati a questo punto si abbassa drasticamente la temperatura del gas a -163°C, al dì sotto della temperatura di ebollizione del metano, principale componente del gas naturale.
Con tubi criogenici, situati su pontili di caricamento, viene iniettato il gas naturale liquefatto all’interno di serbatoi posti sulle navi metaniere. Queste particolari navi possono trasportare dai 150 ai 200 mila metri cubi di metano, e ne esistono di due tipologie:
- Il primo esempio è quello di nave con serbatoi integrati sviluppati dalla Gaztransport & Technigaz. Per questa tipologia esistono 2 versioni: quella della Technigaz con serbatoi costituiti da una barriera primaria elastica, formata da una membrana con nervature realizzata con lastre di acciaio; la disposizione delle lastre forma due ordini di nervature ortogonali tra di loro ed hanno la funzione di ridurre le sollecitazioni termiche. La barriera secondaria è realizzata con un materiale composito, il “triplex”, costituito da un foglio di alluminio in un wafer di tessuto di fibre di vetro. Il serbatoio è fissato allo scafo interno con una schiuma di poliuretano rinforzata con fibre di vetro. La tipologia messa a punto dalla Gaztransport invece prevede due barriere costituite da fasciame piano saldato, fatto di una particolare lega metallica di acciaio e nickel, chiamato invar. Tra le due barriere sono presenti dei pannelli isolanti e delle camere d’aria, nella quali vieni iniettato dell’azoto liquido per mantenere la temperatura criogenica del gas naturale. In questo caso il serbatoio è tenuto allo scafo interno con delle scatole di isolamento termico in legno di balsa riempite di perlite.
- Altro esempio di nave metaniera e con serbatoi autoportanti: la società Moss Rosenberg affrontò il problema della resistenza alle sollecitazioni indotte dal peso del gas naturale nei serbatoi, per risolvere progettò metaniere con 4 o 6 serbatoi sferici. Le sfere sono isolate con uno strato di materiale isolante, tra di esse viene fatta passare un’intercapedine riempita con azoto per aumentare la capacità isolante e mantenere bassa la temperatura del serbatoio. Ogni sfera è sostenuta da una camicia cilindrica che poggia sullo scafo della nave; quest’ultimo viene protetto da eventuali fughe di gas con una barriera secondaria posta alla base delle sfere.
La metaniera trasporta il suo carico di GNL sino all’impianto di rigassificazione; dopo essere state ancorate e aver effettuato la connessione ai bracci di scarico degli impianti del porto, iniziano a trasferire il GNL nei serbatoi di stoccaggio. Gli impianti di rigassificazione possono trovarsi in zone portuali, quindi parliamo di un impianto onshore sulla terraferma, oppure di una piattaforma, appoggiata sul fondo marino, che prende il nome di offshore gravity based, o ancora di una floating storage and regasification unit, FSRU, una nave metaniera, convertita per la rigassificazione, ancorata al fondale marino, ma questa tipologia la vedremo più avanti.
Con le pompe di bordo della nave metaniera, viene scaricato il GNL nei serbatoi dell’impianto, per un carico standard ci voglio all’incirca 12 ore. Il GNL viene immagazzinato sempre in forma liquida ecco perché vengono adottati degli speciali tubi criogenici, che sono in grado di gestire e mantenere la temperatura di -163°C del gas liquefatto.
Il GNL viene immagazzinato in serbatoi a doppio guscio a pressione atmosferica. Il guscio interno, a contatto con il GNL, è realizzato in acciai speciali con il 9% di nichel per evitare problemi di rottura dovuti alle basse temperature. Il guscio esterno invece è costituito da calcestruzzo precompresso. Tra l’intercapedine dei due gusci è presente un rivestimento isolante ed un altro rivestimento sul fondo in schiuma di vetro. Tutti i serbatoi di GNL sono di forma cilindrica e posano su di una base dove sono presenti isolatori sismici, per evitare rotture e perdite durante gli scossoni di un terremoto. Le fasi di riempimento ed estrazione del GNL avvengono sulla parte superiore, con l’ausilio di una pompa ad immersione; il soffitto è costituito da uno strato di isolamento tenuto da cavi di sospensione e un rivestimento in acciaio, ricoperti da una parete in calcestruzzo rinforzato. I serbatoi possono essere interrati, per avere un minore impatto visivo, ma hanno costi di realizzazione e manutenzione molto elevati, ecco perché si preferisce installarli in superficie, dove i costi sono decisamente più contenuti; la capacità di un serbatoio può variare tra i 7.000 metricubi e i 160.000 metri cubi.
Una volta stoccato il GNL nei serbatoi, può procedere la fase di rigassificazione, in impianti che effettuano una vaporizzazione del gas liquefatto. Questo trattamento è molto delicato e può essere effettuato con diverse tecnologie, che si distinguono in base alla temperatura di esercizio, ovvero processi a temperatura ambiente e temperatura superiore a quella ambiente.
Per il processo con temperatura ambiente si utilizza un Vaporizzatore ad acqua di mare (open rack vaporizer). Il funzionamento è molto semplice: all’interno del vaporizzatore ci sono fasci tubieri verticali, realizzati in lega di alluminio e rivestiti con una lega di zinco per prevenire i fenomeni di corrosioni indotti dal sale marino, attraverso i quali fluisce il GNL con un flusso che va dal basso verso l’alto; su questi tubi viene fatta cadere a pioggia dell’acqua marina a temperatura ambiente, che trasferisce il suo calore al fascio tubiero permettendo al suo interno la vaporizzazione del GNL. L’acqua marina successivamente viene raccolta per essere restituita al mare alla temperatura di 4-5 °C, facendo particolare attenzione al contenimento di sostanze nocive per l’ambiente. Si tratta di una tecnologia molto collaudata nell’industria del GNL, usata soprattutto in Europa, che non utilizzando una fonte di calore per riscaldare il GNL consente di ridurre le emissioni di Co2 nell’atmosfera.
Questa tecnologia viene utilizzata anche su navi metaniere convertite in FSRU, ovvero Floating Storage and Regasification Unit. Questa particolare imbarcazione permette contemporaneamente il trasporto e la rigassificazione del GNL una volta arrivata nella zona di scarico in prossimità delle coste. Queste navi sono di una lunghezza che variano dai 250 ai 280 metri e larghe intorno ai 40 metri, con una capacità di circa 140.000 metricubi ed una produzione annua di 2,5/3 milioni di tonnellate.
Per il processo con temperatura superiore a quella ambiente si utilizza un Vaporizzatore a fiamma sommersa (submerged combustion vaporizer), vediamo insieme come funziona: per i sistemi a combustione sommersa troviamo un bruciatore posto in un bagno di acqua, la quale costituisce il fluido che riscalderà il GNL. Per la combustione del bruciatore si utilizza una piccola quantità del gas naturale importato, generalmente l’1,5%, che viene precedentemente preriscaldato. I gas caldi prodotti vengono convogliati tramite un sistema di distribuzione all’interno del bagno di acqua calda, il quale è attraversato da un fascio tubiero che trasporta il GNL che vaporizza all’interno del fascio stesso. Il gas vaporizzato viene avviato alla fase di compressione e allo stoccaggio in serbatoi sferici, e in seguito verrà immesso nella rete di trasporto e distribuzione.
Siamo così giunti alla fine del nostro video. Abbiamo visto tutte le tappe della filiera del gas naturale liquido, dalla liquefazione negli impianti costieri alla sua rigassificazione con tecnologie in continua evoluzione.
Il GNL viene immagazzinato in serbatoi a doppio guscio a pressione atmosferica. Il guscio interno, a contatto con il GNL, è realizzato in acciai speciali con il 9% di nichel per evitare problemi di rottura dovuti alle basse temperature. Il guscio esterno invece è costituito da calcestruzzo precompresso. Tra l’intercapedine dei due gusci è presente un rivestimento isolante ed un altro rivestimento sul fondo in schiuma di vetro. Tutti i serbatoi di GNL sono di forma cilindrica e posano su di una base dove sono presenti isolatori sismici, per evitare rotture e perdite durante gli scossoni di un terremoto. Le fasi di riempimento ed estrazione del GNL avvengono sulla parte superiore, con l’ausilio di una pompa ad immersione; il soffitto è costituito da uno strato di isolamento tenuto da cavi di sospensione e un rivestimento in acciaio, ricoperti da una parete in calcestruzzo rinforzato. I serbatoi possono essere interrati, per avere un minore impatto visivo, ma hanno costi di realizzazione e manutenzione molto elevati, ecco perché si preferisce installarli in superficie, dove i costi sono decisamente più contenuti; la capacità di un serbatoio può variare tra i 7.000 metricubi e i 160.000 metri cubi.
Una volta stoccato il GNL nei serbatoi, può procedere la fase di rigassificazione, in impianti che effettuano una vaporizzazione del gas liquefatto. Questo trattamento è molto delicato e può essere effettuato con diverse tecnologie, che si distinguono in base alla temperatura di esercizio, ovvero processi a temperatura ambiente e temperatura superiore a quella ambiente.
Per il processo con temperatura ambiente si utilizza un Vaporizzatore ad acqua di mare (open rack vaporizer). Il funzionamento è molto semplice: all’interno del vaporizzatore ci sono fasci tubieri verticali, realizzati in lega di alluminio e rivestiti con una lega di zinco per prevenire i fenomeni di corrosioni indotti dal sale marino, attraverso i quali fluisce il GNL con un flusso che va dal basso verso l’alto; su questi tubi viene fatta cadere a pioggia dell’acqua marina a temperatura ambiente, che trasferisce il suo calore al fascio tubiero permettendo al suo interno la vaporizzazione del GNL. L’acqua marina successivamente viene raccolta per essere restituita al mare alla temperatura di 4-5 °C, facendo particolare attenzione al contenimento di sostanze nocive per l’ambiente. Si tratta di una tecnologia molto collaudata nell’industria del GNL, usata soprattutto in Europa, che non utilizzando una fonte di calore per riscaldare il GNL consente di ridurre le emissioni di Co2 nell’atmosfera.
Questa tecnologia viene utilizzata anche su navi metaniere convertite in FSRU, ovvero Floating Storage and Regasification Unit. Questa particolare imbarcazione permette contemporaneamente il trasporto e la rigassificazione del GNL una volta arrivata nella zona di scarico in prossimità delle coste. Queste navi sono di una lunghezza che variano dai 250 ai 280 metri e larghe intorno ai 40 metri, con una capacità di circa 140.000 metricubi ed una produzione annua di 2,5/3 milioni di tonnellate.
Per il processo con temperatura superiore a quella ambiente si utilizza un Vaporizzatore a fiamma sommersa (submerged combustion vaporizer), vediamo insieme come funziona: per i sistemi a combustione sommersa troviamo un bruciatore posto in un bagno di acqua, la quale costituisce il fluido che riscalderà il GNL. Per la combustione del bruciatore si utilizza una piccola quantità del gas naturale importato, generalmente l’1,5%, che viene precedentemente preriscaldato. I gas caldi prodotti vengono convogliati tramite un sistema di distribuzione all’interno del bagno di acqua calda, il quale è attraversato da un fascio tubiero che trasporta il GNL che vaporizza all’interno del fascio stesso. Il gas vaporizzato viene avviato alla fase di compressione e allo stoccaggio in serbatoi sferici, e in seguito verrà immesso nella rete di trasporto e distribuzione.
Siamo così giunti alla fine del nostro video. Abbiamo visto tutte le tappe della filiera del gas naturale liquido, dalla liquefazione negli impianti costieri alla sua rigassificazione con tecnologie in continua evoluzione.